So wird der Backforce One hergestellt – Marco besucht die Produktion von Interstuhl!
- Autor: Marco Nykamp
- Zuletzt aktualisiert: 07.04.2023
Einen Bericht wie diesen gibt es heute zum ersten Mal. Es ist das erste Mal, dass ich mir die Produktion eines Gaming Stuhls selbst ansehen durfte und diese auch filmen durfte. Voller Stolz kann ich euch also heute recht exklusive Eindrücke in die Herstellung des Backforce One präsentieren.
Der Gaming Stuhl wird wie ihr in meinem ▷ Backforce One Test & Backforce One Plus Test schon lesen konntet, von Interstuhl in Meßstetten Tieringen produziert – genau wie der neue Backforce V.
Interstuhl selbst hat etwa 650 Mitarbeiter und ist nach wie vor ein inhabergeführter Familienbetrieb. Die Firma gibt es schon seit über 50 Jahren und somit sind auch über 50 Jahre Erfahrung in die Konzeption und Umsetzung des Backforce One geflossen. Einblicke in die Produktion dieses Stuhls Made in Germany bekommt ihr nun per Video & in diesem Bericht. Viel Spaß!
Inhaltsverzeichnis
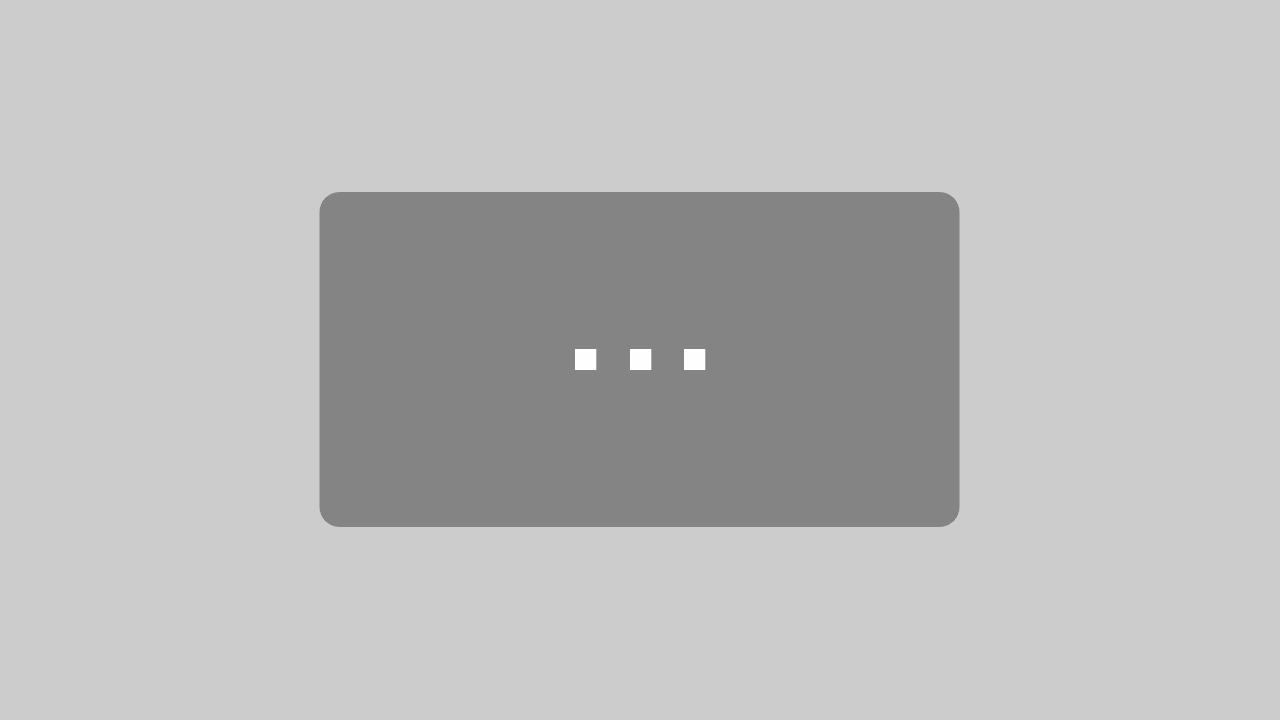
Mit dem Laden des Videos akzeptieren Sie die Datenschutzerklärung von YouTube.
Mehr erfahren
Natürlich kann ich euch nicht jeden einzelnen Produktionsschritt bis zum fertigen Endprodukt zeigen. Einige sehr interessante Einblicke sind aber in jedem Fall dabei.
Angebote sichern: Zum neuen Backforce One geht's hier:
Die Näherei - Steppmuster der Rückenlehne
Wir beginnen mit dem Schulterbereich der Rückenlehne. Genauer gesagt schauen wir uns an, wie die Rückenlehne ihr sehr ansehnliches Design erhält.
Das ist der Arbeitsplatz einer Näherin bzw. eines Nähers bei Interstuhl.
Hier sehen wir Schnittmuster für die einzelnen Bezugskomponenten des BF One.
Um dieses schöne Steppmuster zu erzeugen, wird folgendermaßen gearbeitet:
Zu aller erst aber wird eine Schablone aufgelegt und es wird ein Muster eingezeichnet. Auf jeder dieser eingezeichneten Linien wird gleich genäht, um das Muster zu erzeugen.
Unter dem Kunstleder befindet sich ein Schaum. Der ist dafür da, dass sich am Ende das Steppmuster schön abzeichnet. Dadurch, dass unter dem aufgenähten Leder Schaum ist, entstehen die gepolsterten Wölbungen.
Schaumanlage - So werden Sitzschaum & Rückenschaum hergestellt
In diesem Abschnitt schauen wir uns an, wie die Polsterschäume für die Sitzfläche & Rückenlehne produziert werden.
Das ist eine Schaumanlage von oben. In die Formen, die rein von der Funktion einem Waffeleisen ähneln, wird die Grundmasse für den Polsterschaum eingefüllt.
Ein Roboterarm befüllt die Formen selbstständig mit dem Grundmaterial für Polsterschäume.
Es dauert 8 Minuten und braucht 60°C, bis der Polsterschaum fertig ist.
Thema Nachhaltigkeit: Normalerweise werden diese Formen mit Silikon benetzt, damit sich der fertige Schaum gut lösen lässt. Hier hat man sich aber irgendwann gefragt, ob es nicht auch mit Wachs funktioniert, um die Produktion wieder einen Tacken nachhaltiger zu gestalten. Man hat erkannt, dass es mit Wachs problemlos funktioniert, deshalb werden die Formen hier mit Wachs benetzt.
Im Schaum der Sitzfläche befinden sich Luftlöcher. Diese sorgen dafür, dass beim Anlehnen die Luft entweicht. Das hilft dabei, die Polsterung so atmungsaktiv wie möglich gestalten.
Die Schäume werden hier kurzfristig gelagert, bis sie im Anschluss direkt weiterverarbeitet werden.
Angebote sichern: Zum neuen Backforce One geht's hier:
Produktion des Rückenschaums
Jetzt schauen wir uns an, wie der Polsterschaum für die Rückenlehne produziert wird.
Das ist das Werkzeug, also die Form für die Herstellung des Rückenpolsters, in die gleich die flüssige Grundmasse eingefüllt wird.
Vorher muss aber zuerst an den dafür vorgesehenen Stellen Klettband eingelegt werden. An dem Klettband wird später der Bezug fixiert, das werden wir noch sehen. Beim Ausschäumen wird sich das Klettband mit dem Schaum verbinden.
Nun wird die flüssige Masse in die Form gefüllt und verteilt. Der Prozess ist vergleichbar mit einem Waffeleisen. Es kommt wenig Grundstoff hinein, der dann durch die mittels Warmwasser aufgeheizte Form innerhalb von 8 Minuten sozusagen aufgeht.
8 Minuten später können wir uns das Produkt ansehen:
Die Überstände am Rand werden natürlich noch abgeschnitten, um eine komplett saubere Form zu erhalten.
Man sieht auch sehr schön, wie sich Polster & Klettband miteinander verbunden haben.
Verarbeitung der Rückenlehne in Polsterei
Jetzt schauen wir uns an, wie Richard die Rückenlehne bezieht. Richard hat seine Ausbildung bei Interstuhl gemacht und ist seitdem dort angestellt.
Das Schaumteil wurde bereits mit dem Rückenholz versehen.
Hier fixiert er den Bezug an dem Hakenband. Man sagt ja eigentlich meistens Klettband, aber für Klett braucht man ja zwei Bänder: Ein Mal das Flauschband und dann noch das Hakenband, das das Flauschband fixiert.
Die blauen Bänder sind Hakenbänder. Die Naht wird fixiert. Ohne das Hakenband würde sich das Material auf Dauer ausdehnen und verrutschen. Der Bezug würde wie ein Sack über der Rückenlehne hängen.
Während des Prozesses wird ständig kontrolliert, ob alles so sitzt wie es soll. Alles muss gleichmäßig sitzen, es wird nicht wild rumgetackert. Der Prozess ist wesentlich schwerer, als es aussieht.
Dieser Schutz auf den Fingern ist übrigens dafür da, dass die Materialien nicht in die Finger schneiden. Ein Handschuh wäre zu hinderlich, das Feingefühl ginge verloren. Deshalb gibt es solch einen Fingerkuppenschutz.
Auf der Rückseite der Rückenlehne wird nun noch ein dünner Schaum angebracht, auf dem wiederum eine in diesem Falle blaue Matte angebracht wird.
Je nach gewählter Stuhlfarbe unterscheidet sich natürlich auch die Farbe dieser Komponente – bei einem orangen Stuhl ist sie entsprechend Orange. Die später zu montierende Kunststoffverkleidung hat Aussparungen, sodass man diese Farbe beim Endprodukt sieht.
Ein in meinen Augen wichtiger und interessanter Schritt. Denn besonders durch diesen Prozess wird der Backforce One auch von hinten ein Hingucker. Wenn wir auf dem Stuhl sitzen, bekommen wir vom Design schließlich nicht viel mit.
Sobald wir aber nicht mehr am Rechner sind und den Stuhl an den Tisch schieben, macht er von hinten ein richtig gutes Bild. Wo die meisten Gaming Stühle von hinten schlicht schwarz sind, sieht der Backforce One eben genau dort gut aus, wo man es am häufigsten sieht.
Die Kunststoffverkleidung der Rückenlehne wird hier nur angehalten, um zu schauen, ob alles stimmt. Es handelt sich hier nur um ein Muster, die tatsächliche Montage erfolgt in einem anderen Bereich.
Zum Schluss wird nochmals gedämpft. Durch das Dämpfen zieht sich das Material zusätzlich zusammen. Nun ist die Rückenlehne fertig für den nächsten Schritt!
Angebote sichern: Zum neuen Backforce One geht's hier:
Schweißerei - ein unzerstörbarer Rückenbügel
Als nächstes kamen wir in der Schweißerei vorbei. Schweißvorgänge gab es nicht zu betrachten, allerdings haben wir uns den Rückenbügel des Backforce One angesehen, der Rückenlehne und Sitzmechanik an der Rückenlehne verbindet.
Dieses Teil wird in der Schweißerei nur gestanzt. Dir Formgebung ist genau so gewollt, sie sorgt für eine deutlich höhere Stabilität, die in Kombination mit der Stahldicke und der Konstruktion für die Ewigkeit gemacht ist.
An dem Teil kann man biegen und brechen wie man will, es bewegt sich keinen Millimeter.
Endmontage - die letzten Schritte
Wir sind nun in der Endmontage angekommen, in der die letzten Schritte in der Produktion des Backforce vorgenommen werden.
Hier sehen wir die Rückenlehne, auf der gleich die Kunststoffverkleidung angebracht wird.
In diesem Schritt wird die Mechanik an den Stuhl montiert. Diesen Prozess nennt man Hochzeit – so wie bei den Autobauern, wenn Getriebe & Karosserie verbunden werden. Bei den Autobauern wie bei den Stuhlbauern nennt man also die Zusammenführung der Herzstücke des Produktes „Hochzeit“.
Am Ende prüft der Mitarbeiter den Stuhl nochmal auf seine Funktionen, schaut also ob alles ordnungsgemäß funktioniert.
Schön finde ich hier auch nebenbei die Verpackung. Diese kann nämlich für den Aufbau des Stuhls genutzt werden. Man legt die Rückenlehne gemäß der eingezeichneten Silhouette auf und kann so problemlos die Sitzmechanik montieren, ohne die Schraublöcher groß ausbalancieren zu müssen.
Das kann manchmal echt nervig sein. Die Idee dazu hatte einer der sehr engagierten Mitarbeiter, die Idee wurde erfolgreich umgesetzt und ist heute eine angenehme Montagehilfe für jeden Backforce-One-Käufer.
Versand und Qualitätskontrolle
Diese Abteilung fand ich persönlich auch sehr interessant. Der Backforce One wird hier zwar nicht bearbeitet, sondern nur einige der vielen anderen Stühle aus dem Hause Interstuhl – aber dennoch eine sehr spannende Sache.
Auch hier prüft ein Mitarbeiter jeden Stuhl auf seine Funktion.
Anschließend kommt der Stuhl in ein Versandschiff aus Pappe und kommt auf’s Rollband. Und hier wird’s interessant: Der Stuhl muss nämlich jetzt in die Versandabteilung, welche im übernächsten Gebäudeteil liegt.
Der Stuhl fährt hier also den Aufzug runter und wird durch die Katakomben in den übernächsten Gebäudeteil überführt.
Hier kommt er wieder hoch, um an der Decke entlang zur Versandabteilung transportiert zu werden.
Angebote sichern: Zum neuen Backforce One geht's hier:
Das Labor - Der "hauseigene TÜV"
Und Jetzt können wir uns noch ansehen, wieso es sich Interstuhl unter anderem leisten kann, ganz selbstbewusst 10 Jahre Garantie auf den Backforce One zu geben.
Denn hier seht ihr gerade das Labor von Interstuhl, in dem jeder Stuhl, schon bevor er auf den Markt kommt, ausgiebig getestet werden kann.
Hier wird also jede Komponente den täglichen Belastungen in simulierter Form ausgesetzt. Und die Prozesse die ihr hier seht, müsst ihr euch jetzt über viele Stunden vorstellen. Es wird sich hier also in einem festgelegten Zeitraum beispielsweise mehrere 10-Tausend Mal angelehnt, um absolut sicher zu gehen, dass der Stuhl in seiner Konstruktion funktioniert.
So kann man das Produkt schon vor dem Marktstart nahezu in Richtung Perfektion optimieren, weil man viele Fehlerquellen bereits im Voraus ausmerzt und so ein ausgereiftes & robustes Produkt auf den Markt bringen kann.
Hier wird auch wirklich alles getestet: Auf den Sitzflächen wird häufiges Hinsetzen mit entsprechenden Gewichten simuliert, die Rollen werden mit schweren Gewichten auf ihre Belastbarkeit geprüft, Rückenlehnen & Mechaniken werden starken Belastungen ausgesetzt und auch die Bezugsstoffe werden Abriebtests unterzogen.
Das Labor ist für Interstuhl quasi der hauseigene TÜV.
Nachhaltigkeit & Mitarbeiterzufriedenheit bei Interstuhl
An vielen Stellen war ich fasziniert, wie nachhaltig Interstuhl arbeitet und wie man hier immer wieder neue Dinge entdeckt, um maximal ressourcenschonend zu arbeiten. Ich habe ja weiter oben schon angemerkt, dass die Formen für die Schäume statt mit einem Kunststoff wie Silikon mit einem Naturstoff wie Wachs benetzt werden.
Abgesehen davon wird nach Just-in-Time-Prinzip hergestellt. Die Teile werden kaum noch eingelagert, sondern produziert bzw. angeliefert und direkt weiterverarbeitet.
So musste man früher in der herkömmlichen Produktion massenweise vorproduzieren und auf Lager legen. Gewisse vorproduzierte Komponenten müssen dann eingepackt werden, eingelagert werden und bei Nutzung wieder ausgepackt werden.
Beim Just-in-time-Prinzip werden die produzierten Teile sofort weiterverarbeitet und nicht eingelagert. Das macht die Produktion zum einen effizienter, weil man weniger Lagerkosten hat, zum anderen ist es umweltfreundlicher – weil nicht jedes Teil nach der Produktion in Folie verpackt ins Lager kommt. Das Einpacken & Einlagern entfällt, weniger Plastikmüll wird produziert.
Auch wird die Region unterstützt, man versucht möglichst viele Komponenten von Unternehmen aus der Region zu beziehen. Selbst die Beschläge auf der Toilette kommen von einem Unternehmen aus der Region.
Wasserspender, Kindergarten, Hausaufgabenbetreuung
Sehr positiv ist mir auch aufgefallen, dass die Firma Interstuhl einen firmeneigenen Kindergarten mit samt Ganztags- und Hausaufgabenbetreuung hat, um die Mitarbeiter zu entlasen. Ich kenne hier aus meiner Region einige große Firmen, aber das bietet keine von ihnen. Das hat mich sehr überrascht.
Außerdem stehen überall auf dem Produktionsgelände Wasserspender, an denen die Mitarbeitet natürlich kostenlos Wasser abfüllen können. Dazu hat jeder Mitarbeiter eine Flasche mit dem eigenen Namen drauf. Hier kümmert man sich tatsächlich gut um seine Mitarbeiter. Und wenn ein Mitarbeiter Nachwuchs bekommt, wird auf dem Firmengelände ein Baum gepflanzt.
Ist der Backforce One wirklich sein Geld wert?
So einen Stuhl zu konstruieren ist sehr teuer. Allein die Werkzeuge, das haben mir schon mehrere Hersteller bestätigt, sind unwahrscheinlich teuer. Man muss ein Werkzeug konstruieren, mit dem sich beispielsweise die Rückenlehnenverkleidung gießen lässt. Solche Werkzeuge sind unheimlich teuer.
Und gerade weil solche Werkzeuge so teuer sind, sieht man auch so extrem selten Stühle wie diesen – eine Stahlkonstruktion zu polstern und zu beziehen ist einfach wesentlich kostengünstiger.
Und jetzt muss man sich eben Gedanken machen: Kaufe ich einen Stuhl aus Fernost, der zu sehr geringen Lohn- und Arbeitskosten produziert wird und seine 400€ kostet – oder gebe ich 100€ mehr aus und bekomme einen aufwändig und kostspielig produzierten Stuhl, der in Deutschland gefertigt wird, recyclebar ist und Arbeitsplätze in Deutschland sichert?
Angebote sichern: Zum neuen Backforce One geht's hier:
Schon bevor ich die Produktion besichtigen durfte, war ich vom Backforce One begeistert. Ein hochqualitativer deutscher Stuhl, der jeden Cent wert ist. Nach meinem Besuch in Meßstetten-Tieringen bin ich davon nur umsomehr überzeugt. Wenn dieser hochklassige Gaming Stuhl zu deinem Körper passt, kann ich dir den Kauf nur ans Herz legen!
Herzlichen Dank an Stefan, Ecki, Holger & das ganze Interstuhl-Team. Der Besuch bei euch hat großen Spaß gemacht!
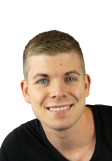
Ich bin Marco Nykamp, TÜV-zertifizierter Ergonomie-Berater und seit 2014 schreibe ich hier über Gaming- und Bürostühle. Du findest hier nur echte, ehrliche & unabhängige Tests & Videos, keinerlei gekaufte oder unehrliche Meinungen. Auch schreibe ich keine Testberichte zu Stühlen, die ich nie wirklich besessen habe.
Weil ich oft auch sehr kritisch mit den Testobjekten bin, bekomme ich nur wenige Stühle for free, den Großteil kaufe ich selbst. Daher wird dieses Projekt durch Affiliate-Programme finanziert. Mehr dazu & über mich findest du hier: Über Marco Nykamp